包装機の段取り替えを減らし、包装数を増やす
BEFORE -改善前-
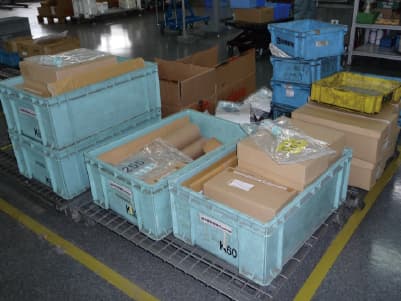
ロット数が50個を超えるような製品は、手作業で袋詰めをするよりも包装機を利用した方が早く作業ができるため、数量によって梱包方法を選んでいます。
<問題>
- 50個位の製品が続くと、機械の稼働時間よりも段取り替えの時間の方が長くなり、効率が落ちる。
- 未包装在庫が増えてしまうと、納期などで優先順位をつけて対応するため、余計に効率が落ちる。
未包装在庫を所定の保管場所に置き切れなくなり、「別の場所で仮保管」→「所定の位置へ戻す」といったムダな作業をすることも多々ありました。
AFTER -改善後-
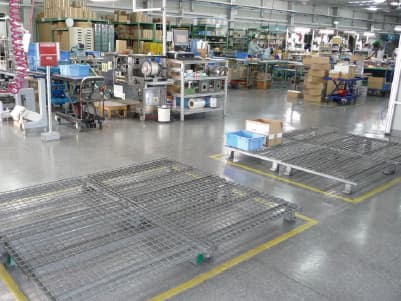
各種類ごとに設定をしていた袋長さを、ある程度共通化することで段取り回数を減らし、一度の段取り替えで多くの種類の包装ができるようにしました。
<効果>
- 機械ごとの梱包状況
縦形包装機…15種類 → 4種類
横形包装機…59種類 → 25種類
品番によっては袋が長くなることで、フィルムの使用量も増えましたが、1回ごとの段取り替えの際に発生している1~3m程の廃棄分が減ったので、トータルの使用量はほとんどかわりませんでした。
メンバーからの一言
今までは常に梱包待ちの製品が控えていましたが、作業効率が上がったことで、終業時間には包装機の前から製品がなくなるようになりました。
手間も保管場所も削減できる良い改善になりました。